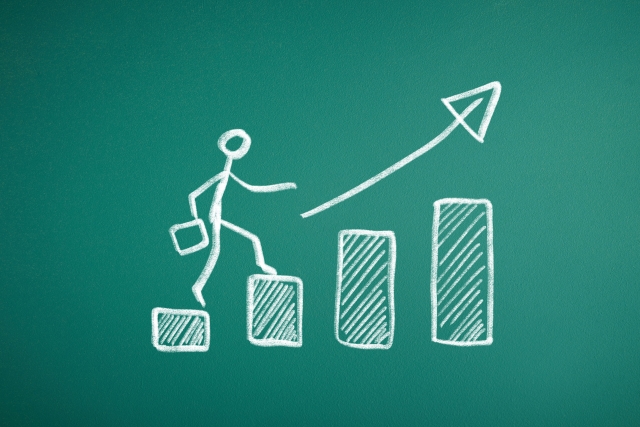
毎年膨大な利益を上げているトヨタ。それほどの利益を生みだしているのは、優れた品質で最新技術を搭載している車を製造販売しているだけでなく、生産効率を究極にまで高めた製造コスト削減も大きな理由です。
その高い生産効率の元となっているのがトヨタ生産方式「カイゼン」です。
カイゼン(改善)は生産現場でよく見られますが、それ以外のところでも非常に多く実践されています。
そこで、ここではトヨタのカイゼンの基本である「ムダ取り」に注目、工場で働いている以外のエンジニアでどのように活用できるかをまとめました。
エンジニアにも生産性向上がさけばれている現在、トヨタ式のムダ取りを実践すれば、生産性向上ができるのです。
トヨタ生産方式のムダ取りを理解し、業務改善・生産性向上に役立たせてもらえばと思います。
トヨタのムダとは
最初にトヨタ生産方式での「ムダ」を説明します。
トヨタ生産方式は、ムダの削減だけでなく、ジャストインタイムやかんばん、見える化など多くの柱があります。
今ではIoTやAIによる生産効率アップを目指していることも多いでしょう。
しかし、ここでは「ムダ取り」を業務効率の基本としておすすめします。
その理由は、
・ムダ取りはカイゼンの基本となるもの
・生産現場だけでなくあらゆる業務に活用可能
・考え方・実施の方法が簡単でわかりやすい
・すぐに実践できる
ことがあげられます。
トヨタ生産方式では、ムダを「7つのムダ」と定義しています。
1. 作り過ぎのムダ
2. 手待ちのムダ
3. 運搬のムダ
4. 加工そのもののムダ
5. 在庫のムダ
6. 動作のムダ
7. 不良を作るムダ
この7つのムダは、「付加価値を高めない」ものとして、削減・削除すべきとされています。
実際に実施しなくても、この7つのムダを覚えておくだけでも、エンジニアとして損はないでしょう。
ノートに書いたりして、常に目につくようにするのも良いでしょう。
ちなみに、簡単に7つを覚える方法として、7つムダの頭文字を取って「カザフ鉄道」とか「飾って豆腐」などがあります。
7つのムダの活用
ここでは工場などの生産現場ではなく、エンジニアがオフィスや研究室などの業務で7つのムダをどう活用するかを考えてみましょう。
作り過ぎのムダ
モノを作り過ぎると仕掛かり品や在庫が増えてしまいます。最悪、それらが売れなくなってしまうと、全くのムダとなってしまいます。
注文に間に合わず潰れてしまうメーカーはないでしょうが、在庫のし過ぎで潰れるメーカーはありますよね。
これをエンジニアに当てはめてみましょう。
例えば、開発のために多くのテストをしているでしょうが、そのテストは本当に必要でしょうか、減らすことができるものはないでしょうか。
サンプルが必要だからといって、余分に作っていないでしょうか。
このように、作りすぎたり、やりすぎていることを探して、削減してみてください。きっとあるはずです。
手待ちのムダ
材料や部品などが不足したり、前工程の遅れなどにより、作業できず待っている状態を手待ちといいます。労賃は発生していますが、商品の生産が遅れしまいますのでムダとなります。
エンジニアの場合、複数の業務をしているので、手待ちが起きることはないでしょう。あえていえば、会議の開始時間になっても遅れるに人がいるため、会議開始が遅れることは手待ちのムダと言えるでしょう。会議には遅れないようにしましょう。
手待ち時間はなくても、業務の進行が待ちになることは多いのではないでしょうか。
プロジェクトの場合は複数のタスクがあり、それぞれが複雑にからみあっている場合が多いでしょう。そのため、あるタスクが遅れてしまったため、プロジェクト全体が遅れてしまうことがあるかも。
そのためには、プロジェクトの計画策定の際に、タスクを細かく洗い出しメンバーを選定、目標から逆算してそれぞれのスケジュールを策定する必要があります。
プロジェクトだけでなく、日常の業務でも、人に振ることは早く依頼することが大事です。他人の都合はコントロールできないもの。ですので、人にしてもらうことは早目に依頼しましょう。そうすることにより、少なくとも自分の手待ちを減らすことができるでしょう。
運搬のムダ
ものを運ぶということはお客様には意味のないことであり価値のないことなのです。
工場で物を一生懸命に運んでいることがありますが実はそれは必要悪で、運ぶという作業をなくしたり、減らして製造することが大事なのです。
製造現場や物流以外、ものを運ぶこと自体は、それほどないでしょう。
しかし、自分も含め、人が動くことも「運搬」と考えてみると「運搬のムダ」は多いではないでしょうか。
そうです、出張や外出はムダが多いと考えてよいでしょう。
もちろん、顔を合わせて話をする必要や、実際に現場に行って確認する必要があるのは事実で、否定しません。
しかし、今ではスカイプで顔を見ながら会議はできます。現場も映像などのデータから情報を得ることが多くなっています。
1時間の打ち合わせのために1日かけるぐらいでしたら、タイムリーに何回もスカイプ会議をする方が良いのではないでしょうか。
加工そのもののムダ
必要以上に加工するものはムダです。
例えば、ネジを必要以上の強度で締めるのはムダなのです。
これに最もあてはまるのが資料作成です。
会議での発表時間は5分なのに、すごい量の資料を作ることはないでしょうか。作る方もムダですが、読む方もムダになります。
また、商品開発においても必要以上の機能はムダになることがあります。お客様にとって必要以上の加工や機能はムダです。
機能をシンプルにすることは、多くの場合に有効な方法ですよ。
在庫のムダ
在庫品を大量に、長時間おいてあることはムダですね。
この在庫のムダはエンジニアにとっては、当てはまることは少ないと言えます。
エンジニアにとって重要な知識や経験は在庫がある方がよいですからね。
トヨタ生産方式では、在庫は少ない方が良いだけでなく、タイミングを重視します。使ったり、出荷するタイミングに在庫があることも重要です。
ですので、商品開発でもプロジェクト推進も早くすれば良いわけではありません。商品ができてから、市場動向などが変わり商品変更をした方が良い場合があるかもしれませんので。
早く進めれば良いわけではないということは認識しておきましょう。
動作のムダ
探したり、持ち替えたりするのはムダです。
製造現場ほどの重要性は低いですが、エンジニアにとってもムダなことは間違いありません。
日頃から、整理整頓をして、ムダを少なくしておきましょう。
不良を作るムダ
これは説明するまでもないですね。せっかく作ったものが不良品で販売できなかったり、手直しが必要であれば、ムダでしかありません。
そう、作り直しもムダです。
資料作成においても、作ったものがダメ出しされては、ムダとなります。
依頼されて実施していたものが、最後になって依頼事項と違っていて、やり直しと言われると、ムダどころか、ショックですよね。
そんなことを防ぐには、早めの確認がおすすめ。
資料なら、概要を早くに作って方向性が間違えてないか先に確認しましょう。
プロジェクトも同様です。頻繁にメンバーと目的を共有して、方向性を間違いないようにしましょう。進捗内容の確認も必要です。
まとめ
トヨタ生産方式による7つのムダを、理解して頂いたと思います。
これらは、IoTが進んだ今日でも、カイゼンや業務効率の考え方の基本となります。
製造現場だけでなく、オフィスで商品開発や設計、研究をしている人でもプロジェクトリーダーでも全てのエンジニアが実際に実践できるものばかりです。
いろいろな、業務効率の手法がありますが、この7つのムダを理解して、実践すれば、業務効率を確実に進めることができます。
実際にトヨタが進めているのですから、間違いないでしょう。
簡単なことから、始めても結構です。明日から、早速実践して下さい。